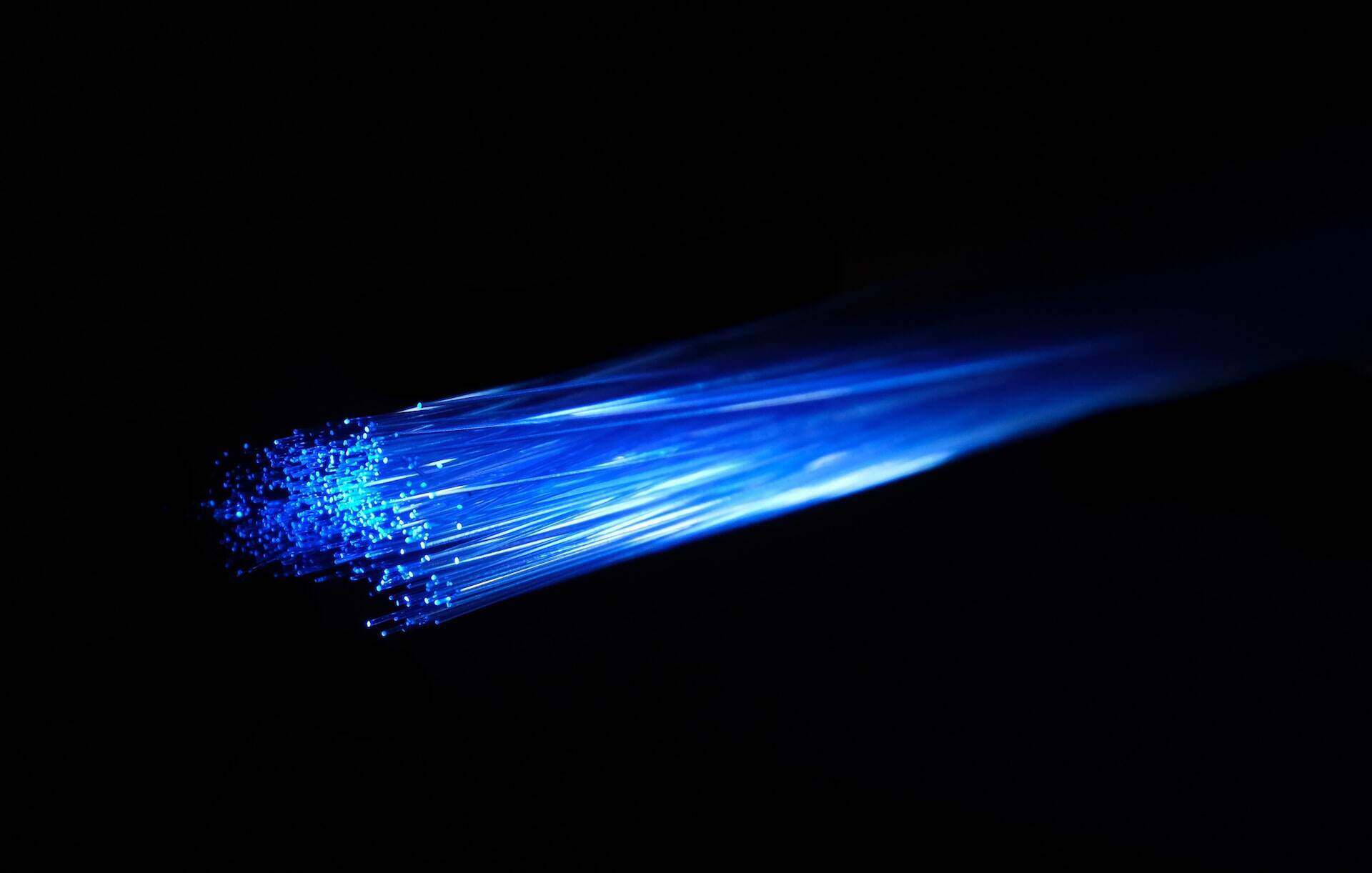
Join Our Team
Shape the future of display technology with us. Join a team that’s pushing boundaries and driving innovation across industries.
Our Perks & Benefits For You
Career Growth
At E3 Displays, we are committed to your professional development. Our supportive environment and opportunities for advancement empower you to reach your full potential.Work-Life Balance
We believe in maintaining a healthy work-life balance, ensuring that our team members can thrive both professionally and personally.Amazing Work Culture
At E3 Displays, we value every team member's voice. Our inclusive, dynamic culture fosters creativity, collaboration, and growth. Join us and thrive with fresh ideas and teamwork.
Comprehensive Health Benefits
We care about the well-being of our employees, offering a range of health benefits to ensure you and your family are supported.
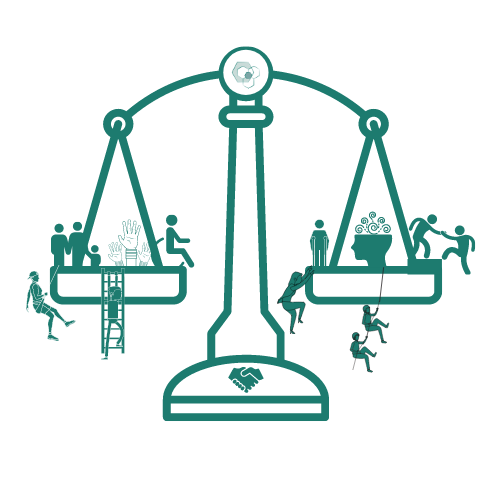
Equal Opportunity
E3 Displays is an Equal Opportunity Employer. We welcome all qualified individuals and do not discriminate based on veteran status, race, gender, sexual orientation, religion, or any other protected category.
Job Roles Available
Business Development Representative, Commercial & Consumer
Business Development Representative, Military & Off-Highway
Business Development Representative, Commercial & Consumer
POSITION OVERVIEW:
The Business Development Representative (BDR) is responsible for the identification, targeting and capture of profitable new business in the Commercial and Consumer segments working on a team led by the Director of Sales and Marketing. The BDR is responsible for generating new leads directly and through channel sales partners, as well as forming business relationships with key prospects and customers. The BDR will solicit RFIs/RFPs and lead cross-functional teams in the preparation and delivery of successful commercial proposals, at which point they will book new orders and participate in negotiating production supply contracts supported by engineering and operations teams.
SPECIFIC RESPONSIBILITIES:
- Identify and develop new sales leads, coordinate proposal activities and build lasting customer relationships in the Commercial and Consumer market segments.
- Organize and conduct presentations of E3D’s value proposition, portfolio products, services and capabilities to current and prospective customers
- Communicate effectively with all levels of external customer management and teams, for both technical and non-technical audiences, including customer executives specifically.
- Support customer and market analysis activity for existing and new product development to better drive the product development and sales activities.
- Advocate for customer expectations internally, with a solution-oriented mindset – collaborating with internal engineering, operations and supply chain teams for success.
- Develop, build and maintain professional business relationships and networks within the assigned portfolio sector, creating strong, long-lasting corporate brand value.
- Contribute to brand awareness and lead generation via targeted outbound marketing.
- Develop a working knowledge of relevant industry partner and competitor activity.
- Forecast revenue and gross profits using Hubspot CRM tools.
- Organize, present, and participate in trade shows as required.
- Maintain and analyze accurate multiyear sales forecast in our Hubspot CRM.
- Ensure reports and other intelligence are provided to internal leadership teams.
- Perform all business development and sales activities direct to customers and indirect with channel partner organizations like sales representative firms and distributors.
- Report on key KPIs related to performance objectives including activity and bookings etc.
- This position requires an eagerness to build relationships and close business face to face by traveling up to 50%.
QUALIFICATIONS:
- Bachelor’s degree in business, finance or engineering and at least 2 years of relevant sales experience w/ strong references.
- Experience working with or selling technical products and services.
- Strong commercial aptitude with proven track record of prioritizing and vetting prospects, leads and closing new customer sales.
- Investing in continuous learning and personal development.
- Eager to hunt for new business, overcome challenges, compete under pressure and close business, face to face with Fortune 1000 executives and technical leaders.
- Available to work onsite in our satellite office in Charlottesville, VA
PERSONAL CHARACTERISTICS:
- High energy level with a positive disposition, self-starter, and results oriented focused.
- Has embedded a passion for competition, resilience, and integrity.
- Excellent verbal communication skills, including the ability to initiate relationships with premier public and private corporate leaders.
BENEFITS:
- High OTE for top performers executing in a supportive, results driven environment.
- Career growth potential within the team at a rapidly growing small business.
- Opportunities to travel internationally (primarily Europe).
- Competitive healthcare, insurance and retirement savings offering.
- World class office in the heart of Charlottesville, VA with relocation financing available
Business Development Representative, Military & Off-Highway
REPORTING:
This position reports to the Director of Sales and Marketing
POSITION OVERVIEW:
The Business Development Representative (BDR) is responsible for the identification, targeting and capture of profitable new business in the Military (ground & marine vehicles + handheld and weapon system controls) and Off-Highway vehicle operator controls and handheld device segments working on a team led by the Director of Sales and Marketing. The BDR is responsible for generating new leads directly and through channel sales partners, as well as forming business relationships with key prospects and customers. The BDR will solicit RFIs/RFPs and lead cross-functional teams in the preparation and delivery of successful commercial proposals, at which point they will book new orders and participate in negotiating production supply contracts supported by engineering and operations teams.
SPECIFIC RESPONSIBILITIES:
- Identify and develop new sales leads, coordinate proposal activities and build lasting customer relationships in the Military and Off-Highway market segments.
- Organize and conduct presentations of E3D’s value proposition, portfolio products, services and capabilities to current and prospective customers
- Communicate effectively with all levels of external customer management and teams, for both technical and non-technical audiences, including customer executives specifically.
- Support customer and market analysis activity for existing and new product development to better drive the product development and sales activities.
- Advocate for customer expectations internally, with a solution-oriented mindset – collaborating with internal engineering, operations and supply chain teams for success.
- Develop, build and maintain professional business relationships and networks within the assigned portfolio sector, creating strong, long-lasting corporate brand value.
- Contribute to brand awareness and lead generation via targeted outbound marketing
- Develop a working knowledge of relevant industry partner and competitor activity
- Forecast revenue and gross profits using Hubspot CRM tools
- Organize, present, and participate in trade shows as required.
- Maintain and analyze accurate multiyear sales forecast in our Hubspot CRM
- Ensure reports and other intelligence are provided to internal leadership teams
- Perform all business development and sales activities direct to customers and indirect with channel partner organizations like sales representative firms and distributors.
- Report on key KPIs related to performance objectives including activity and bookings etc.
- This position requires an eagerness to build relationships and close business face to face by traveling up to 50%
QUALIFICATIONS:
- Bachelor’s degree in business, finance or engineering and at least 2 years of relevant sales experience w/ strong references
- Experience working with or selling technical products and services.
- Strong commercial aptitude with proven track record of prioritizing and vetting prospects, leads and closing new customer sales.
- Investing in continuous learning and personal development.
- Eager to hunt for new business, overcome challenges, compete under pressure and close business, face to face with Fortune 1000 executives and technical leaders.
- Available to work onsite in our satellite office in Charlottesville, VA
PERSONAL CHARACTERISTICS:
- High energy level with a positive disposition, self-starter, and results oriented focused.
- Has embedded a passion for competition, resilience, and integrity.
- Excellent verbal communication skills, including the ability to initiate relationships with premier public and private corporate leaders.
BENEFITS:
- High OTE for top performers executing in a supportive, results driven environment.
- Career growth potential within the team at a rapidly growing small business.
- Opportunities to travel internationally (primarily Europe).
- Competitive healthcare, insurance and retirement savings offering.
- World class office in the heart of Charlottesville, VA with relocation financing available.
What Drives Us
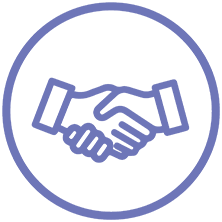
Customers
We are committed to meeting and exceeding our customers’ expectations. We believe the best results stem from a spirit of true partnership which is why we work with our customers in using our skills and experience to fulfill their goals and ideas.
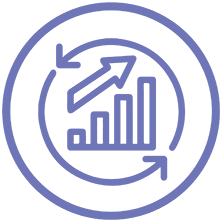
Continuous Improvement
As part of our ORION certification and ISO 9001:2015 standards we are committed to the continuous innovation and improvement of all facets of our business and it’s system. We use lessons learned as a means to continually improve and provide a better customer-centric experience.
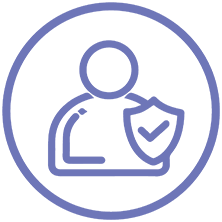
Integrity
We uphold ourselves and all of our employees to uncompromising integrity and act responsibly as well as ethically in both personal and professional relationships. We place a high value on being open and honest with not only our customers but our employees.
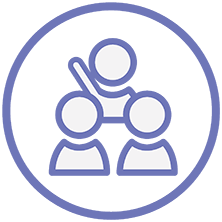
People
We recognize that people are our most important asset for ongoing success and will act accordingly. We are committed to providing competitive results-based compensation, career development, and professional advancement for our employees.
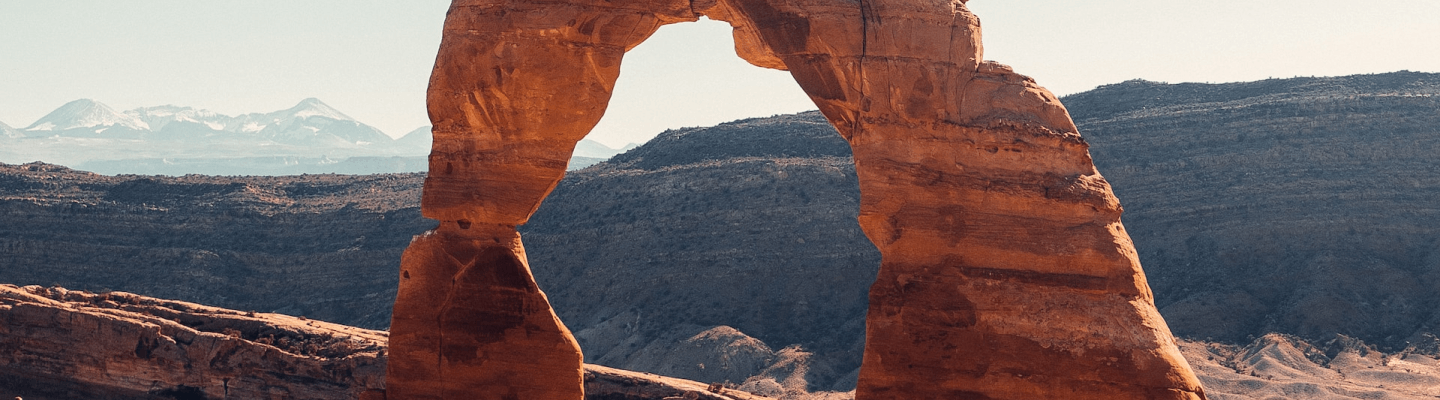