What Makes Optical Bonding Displays Superior in Harsh Environments?
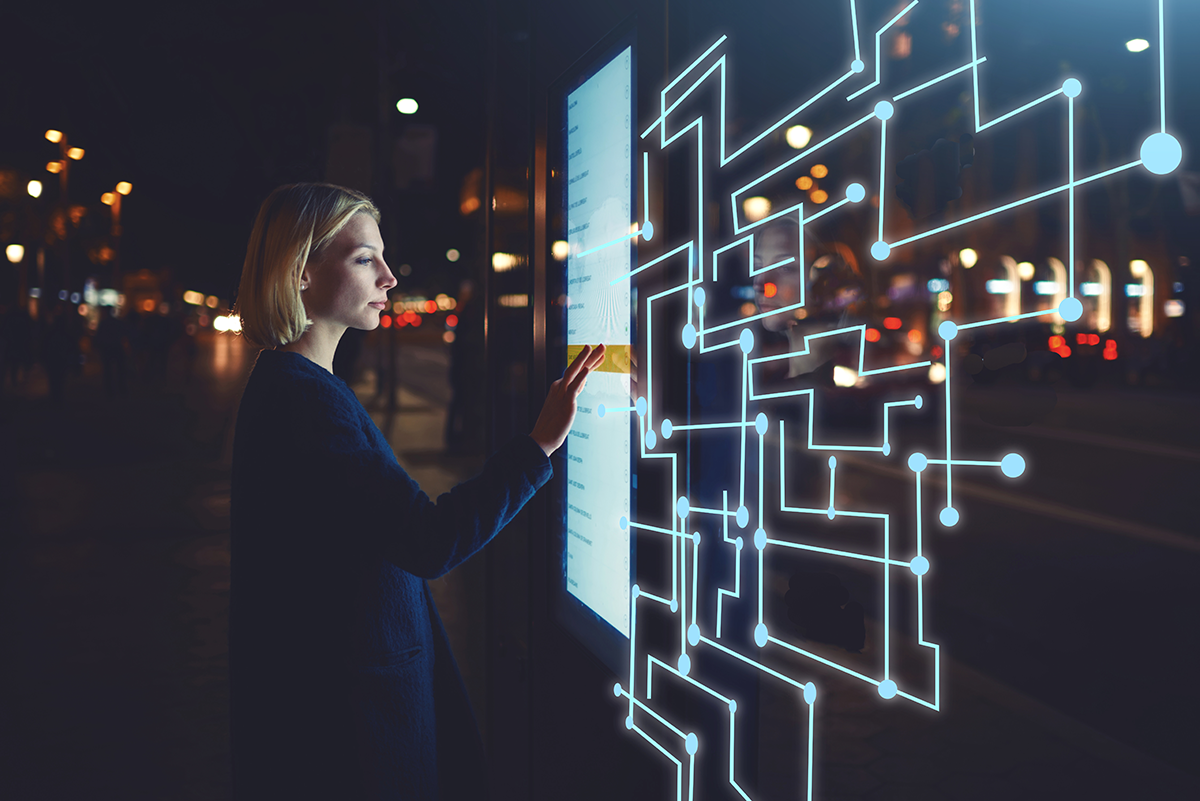
An optical bonding display is meant to perform in demanding industrial, commercial, and outdoor settings. Unlike standard air-gap screen assemblies, optical bonding involves filling the space between the display panel and covering the glass with a solid, optically clear adhesive.
This method improves durability, readability, and mechanical resilience in conditions that would compromise traditional screens.
What Is Optical Bonding?
Optical bonding refers to the process of applying a transparent adhesive—typically silicone or epoxy—to the interface between a display panel (like an LCD or OLED) and a top protective layer, such as cover glass or a touch sensor. By removing the air gap between the display layers, an optical bonding screen minimizes internal reflections, eliminates moisture penetration paths, and increases structural cohesion.
Without bonding, air gaps introduce a secondary reflective surface, which scatters external light and reduces contrast. Bonding addresses this by creating a uniform light path and reducing surface reflection at each interface. This results in sharper images under ambient light and stronger resistance to impact or vibration.
Advantages of Optical Bonding in Harsh Settings
Harsh environments introduce factors that test the limits of display performance. Optical bonding enhances panel stability and screen legibility in field conditions by addressing the mechanical and optical vulnerabilities inherent in traditional displays.
Key benefits of optical bonding displays in rugged settings include:
- Improved sunlight readability through reduced internal reflection and higher perceived contrast.
- Reduced condensation risk, as the absence of air between layers prevents fogging or moisture buildup.
- Greater shock resistance is achieved as bonded layers move as a single unit, preventing delamination or fracture under mechanical stress.
- Better dust protection, especially in applications exposed to particulate matter, dust ingress, or wind-driven debris.
- Increased structural strength, reducing flex and distortion during vibrations or pressure changes.
These improvements are not cosmetic—they directly influence the operational consistency of equipment in sectors where environmental control is minimal or non-existent.
Use Cases That Benefit Most from Bonding
Applications subject to physical or visual challenges benefit significantly from optical bonding services. Industrial automation equipment, field-deployed diagnostic tools, and outdoor information systems require display assemblies that maintain readability and mechanical integrity in a wide range of temperature and lighting conditions.
Common operation points for optical bonding screens include:
- Military equipment exposed to shock, temperature variation, and intense sunlight.
- Medical devices designed for mobile clinics, surgical suites, or cleanrooms requiring disinfectable, sealed surfaces.
- Agricultural and construction vehicles, where exposure to dust, impact, and glare is continuous.
- Transportation terminals with public-facing information displays operating under direct light or elevated heat conditions.
- Marine and aviation systems requiring stable visibility under vibration and variable atmospheric conditions.
Touch interfaces in these environments also benefit from bonding, as interaction stability improves when the touch sensor is bonded directly to the display rather than floating above an air layer.
Integration with Sunlight Readable and Rugged Displays
Optical bonding is not a standalone feature—it is most impactful when integrated with other rugged display technologies. A well-designed optical bonding touchscreen pairs bonded layers with high-brightness panels, EMI shielding, anti-glare coatings, and extended temperature capabilities.
In bright outdoor conditions, internal reflections degrade readability. Bonded displays reduce these reflections, allowing for lower brightness settings while maintaining clarity. This reduction in brightness requirement can lower thermal output and power consumption—an essential consideration for battery-powered or thermally sensitive systems.
For touch screens, bonding enhances touch responsiveness and surface durability. Physical strength increases due to the added bonding layer, allowing for better resistance to scratches and direct impacts without delamination.
E3 Displays: Engineered Optical Bonding Solutions
E3 Displays delivers application-specific optical bonding services for industrial, commercial, and military-grade devices. Bonding techniques are selected based on substrate materials, adhesive properties, display size, and environmental demands.
Projects involving optical bonding touch screens are handled with full attention to clarity, structural alignment, and contamination control. Whether for high-brightness automotive consoles, wearable field units, or HMI systems in hazardous areas, each display module is constructed to meet environmental requirements without compromising display performance.
Bonded assemblies are produced with materials rated for vibration exposure, thermal cycling, and optical uniformity. Touch performance, mechanical integration, and visibility are addressed throughout the entire development process, from early-stage prototyping to final assembly, ensuring the display functions as intended in real-world deployment scenarios.
For industrial, commercial, or field-grade optical bonding display development, contact E3 Displays to initiate a build strategy that aligns with real-world demands.